Architecture and design of the Smart Power Dolly
In April 2021, the commissioning of the AEMPT (Advanced Energy Management PowerTrain) demonstrator could be finalized. One part of the EMS1 vehicle combination is the so-called Smart Power Dolly, an electrically driven and steerable double-axle dolly. It not only supports the reduction of fuel consumption and CO2 emissions while being operated in the EMS1 vehicle combination, but also makes it possible to split vehicles into single units. Remotely controlled the dolly is able to drive without a pulling unit and manoeuvre the semi-trailer to its (un)loading dock.
The Smart Power Dolly was designed and constructed under the direction of Fraunhofer IVI with great support of Van Eck Trailers and ZF Friedrichshafen AG. After some first issues with purchasing a high voltage battery that fulfils the high power demands, all components of the drivetrain, cooling and control system could successfully be specified. The dolly is equipped with an electric portal axle that delivers a peak power of 250 kW and a 73,5 kWh lithium-ion battery. A Local System Management controls the electric powertrain and communicates with the Global Energy and Torque Management System of the towing vehicle. Thus, the dolly reports current traction and braking capabilities to and receives force requests from the truck. Besides, the dolly EBS includes a brake blending function, which can distribute a service brake request between the friction brakes and the electric drive. Communication between vehicle units is realized by an Aeroflex communication protocol based on Automotive Ethernet, which is established in addition to the existing ISO 11992 truck trailer interface. Thus, the bandwidth of the communication connection was extended to 100 Mbit per second (Broad R Reach). The two protocols are combined by an Automotive Ethernet router developed by ZF.
Van Eck Trailers designed and built a completely new base vehicle incorporating the portal axle, the high voltage lithium-ion battery, the two-circuit cooling system and all peripheral components in a very restricted installation space. After the complete system integration, the dolly could be commissioned and made its maiden voyage in manual operation mode using an industrial remote control at the vehicle test circuit of Fraunhofer IVI (Media Center – Fraunhofer IVI).
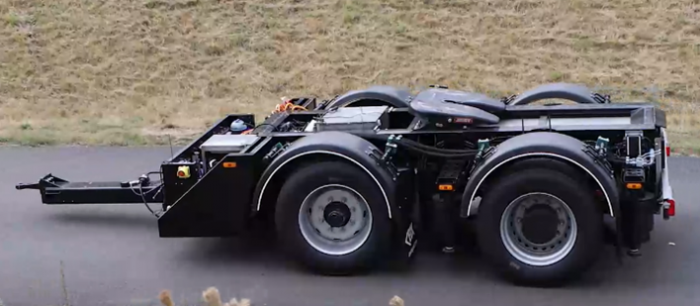
Finally, the Smart Power Dolly was commissioned together with the MAN rigid truck and the electrically driven semi-Trailer (developed in the TRANSFORMERS project) at the ZF test track in Jeversen. Within an extensive test program all power management functions of the AEMPT demonstrator were successfully tested.
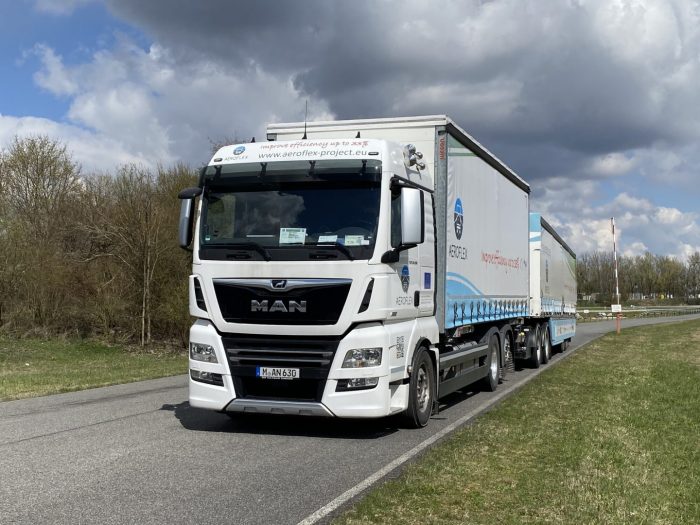